In the dark warehouse,
There's a buzz buzz in the air,
That bee high voltage
Unfortunately, this post is more retro than update. For most of 2024, I spent a lot of time tearing apart electric vehicle battery packs (somewhat safely). They're pretty cool, and since our work dealt with the full range of pack designs, from older hybrids to plug-in electric (PHEV) to full-electric, I felt I also got a decent view of the progressing design trends over the years. For posterity's sake, I wanted to document some of my observations here.
If you're looking for a technical deep dive into battery pack design, there are much better resources out there. In particular, I'd recommend the following channels on Youtube:
Maybe it's a sign of the times. Maybe it's just that video's a better medium for this sort of insight, but I found teardown videos from the sources above to be way more informative and helpful than any manual or research paper as I prepped for hands-on dismantling work.
All in all, the innards are pretty neat:
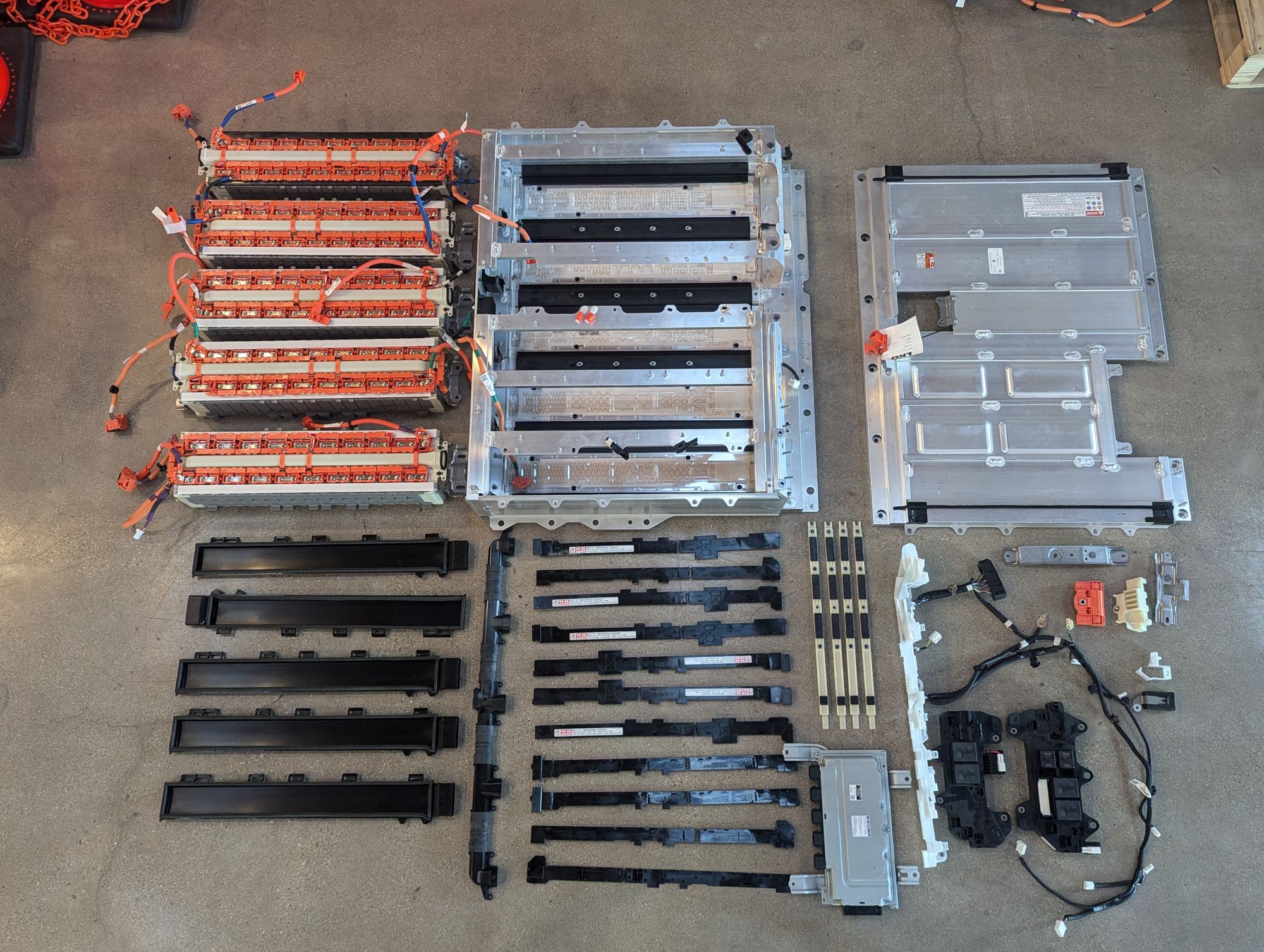
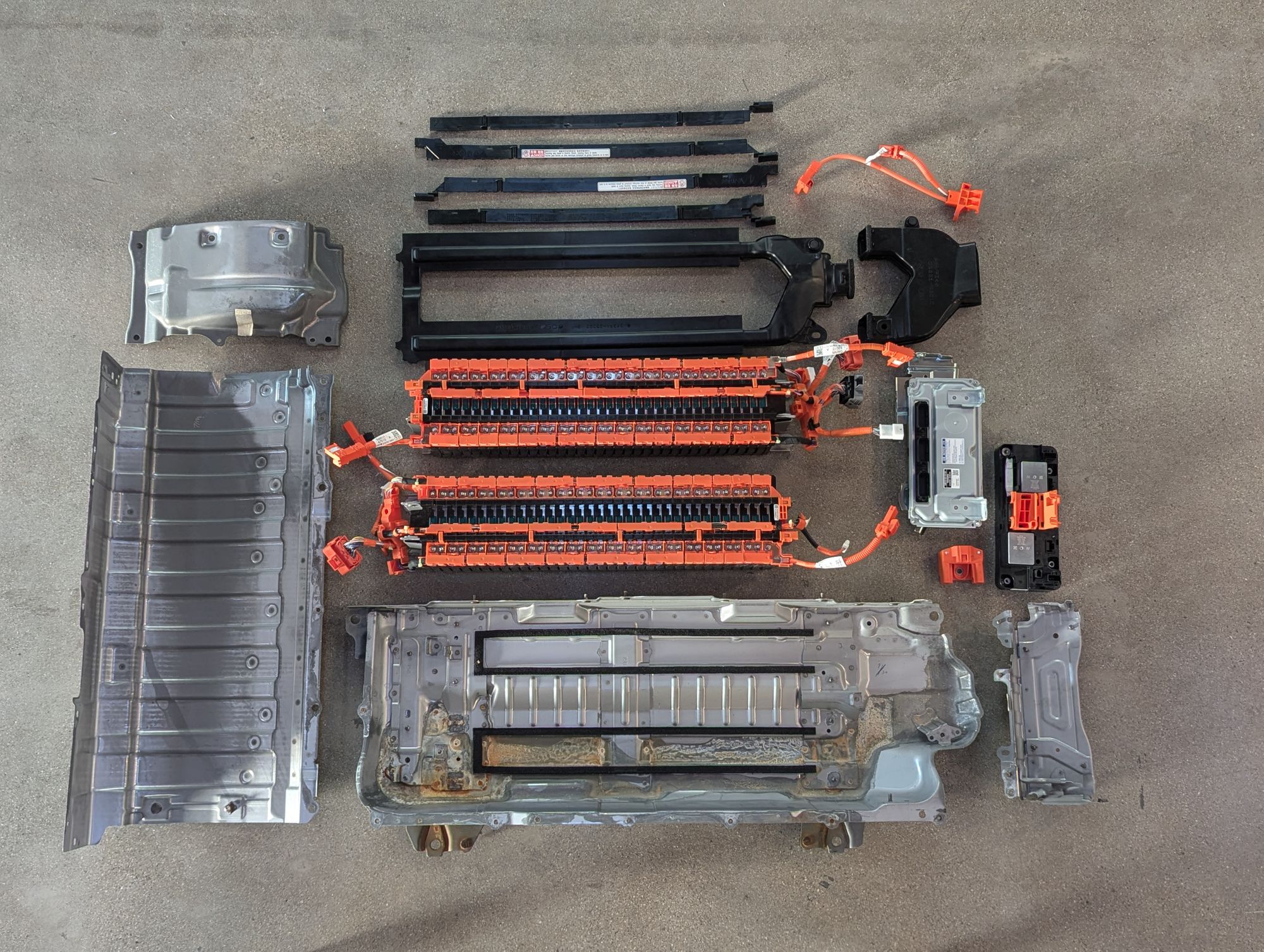
Pack Structure/Enclosure
Hybrids and smaller plug-in hybrids have batteries with primarily aluminum sheet-metal enclosures, whereas you'll see significantly beefier steel enclosures or even billet aluminum frames in larger full-EVs. While there's been more talk and proposals of structural battery packs, which are perhaps more prevalent for cell-to-pack architectures (more on that later), most packs appear to be designed independently of the overall car structure, and they either slot into an interior compartment or bolt onto the underbelly of the vehicle.
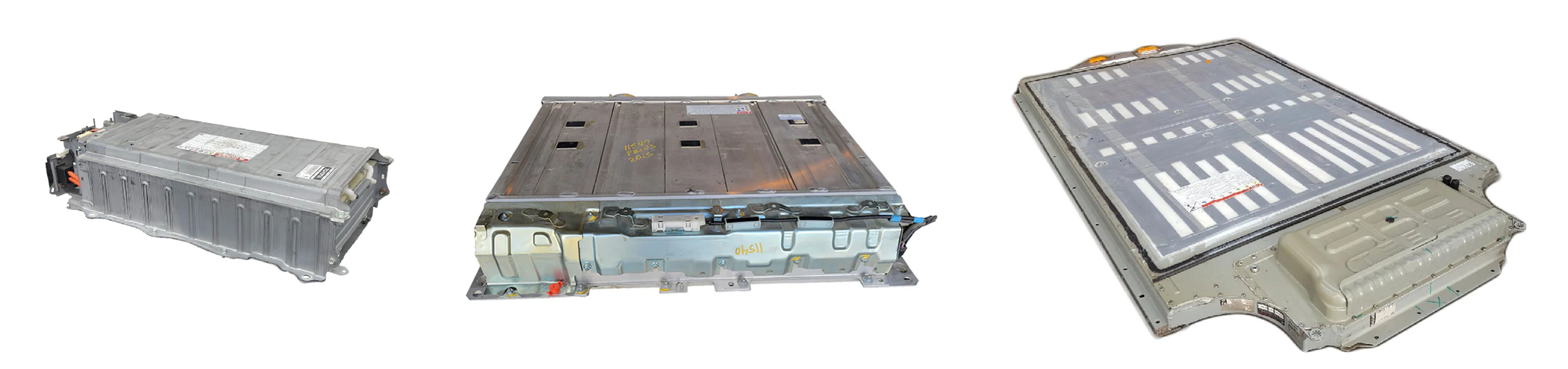
Smaller battery packs are not typically as well-protected against egress or the elements. The Toyota hybrid packs I worked on weren't sealed, and corrosion was a common defect on the interior of the pack, which did not bode well for the various busbars connecting the cells. It seemed like the covers were mostly to prevent technicians from shoving their hands into the cells and wiring. Some plug-in EV packs at least had gaskets and closed up egregious openings. Full-sized EVs took sealing a lot more seriously, and some (annoyingly) apply a fat bead adhesive around the outer boundary of the top lid to both minimize fastener account and really ensure nothings inadvertently gets inside. From what I saw, all top lids, regardless of pack size, were singular stamped metal panels, with rigidity coming almost entirely from embossing.
Speaking of fasteners, most of the battery packs, with the notable exception of Tesla, could be opened with a 10mm socket, which was greatly appreciated. Tesla, on the other hand, not only requires a custom pentalobe socket, but also several different socket and hex bit sizes, not to mention an abrasive cutter to get through the rest of the lid. I can't say that Tesla's packs have embarrassingly low accessibility and reparability in the interest of corporate profit, but I'm also saying I'm not ruling that out.
Modules/Cells
The typical battery pack has cell-to-module-to-pack structure, where the module is a grouping of cells, presumably to improve both assembly and overall structure. While some of the modules may wire their cells in parallel for increased capacity, all modules I saw were wired together in series to produce the pack's final output voltage. In the case of NiMH modules in the Toyota Prius packs, this apparently is especially important as parallel charging can be trickier than with Lithium-ion. Breaking up the pack into modules also makes it easier to disconnect the pack into discrete chunks with significantly smaller and safer voltage.
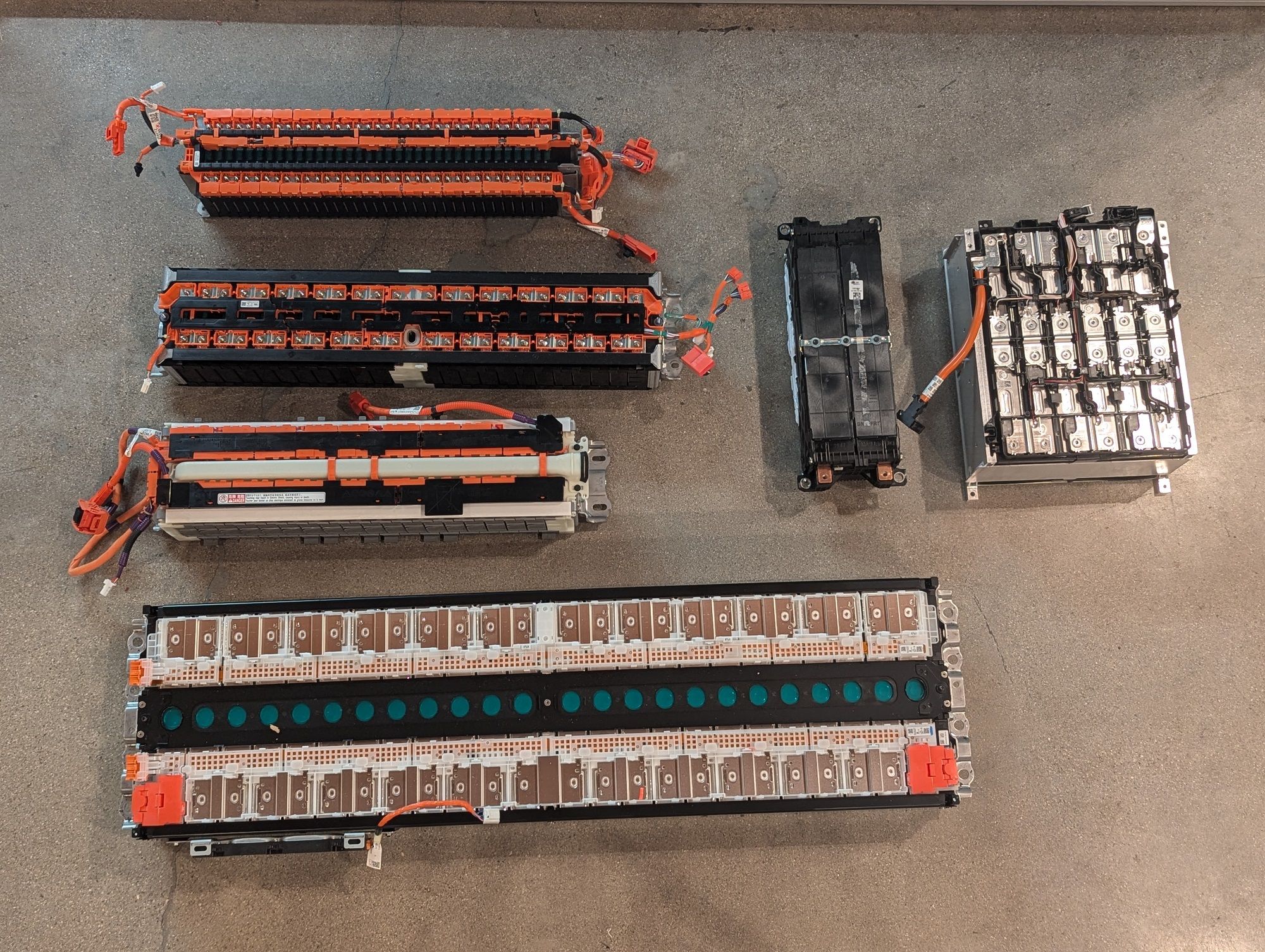
I worked primarily with older models, so most of the modules were comprised of pouch-type cells, which don't have a hard outer casing. This means that cells had to be clamped/packaged within a rigid outer casing. Many of these support structures are welded in place, so you may be able to get the cells out, but that's a one-way, one-time operation. Other cell types include prismatic and cylindrical, the latter of which the public is probably more familiar from consumer electronics.
Cell design has perhaps gotten more attention in recent years with more exotic/robust designs like the BYD Blade and Tesla's 4680, all of which aim to have less susceptibility to thermal runaway, higher energy capacity, better cooling, better structural rigidity/toughness. On that last point, it seems that the latest battery packs are shifting towards a module-less design, where a combination of the latest cells and foam provides the necessary structure. Stateside, this is apparent in teardowns of more recent Rivian and Tesla packs. While the foam reduces initial assembly complexity (and I assume cost), it also substantially complicates the repair and replacement of individual cells.
Safety/Contactors/Busbars
Orange you glad battery safety is a requirement? Across the board, all high voltage lines are terminals are marked super clearly with either orange covers or cable insulation. It's super obvious where the more dangerous areas in a pack are. For the overall pack, it should be noted that the big main contactor relay needs to be triggered for current to flow out of the pack, so a pack disconnected from the main body of the car shouldn't be energized at the main terminals. However, when you open the outer enclosure, all bets are off, so please be safe.
As I hadn't been too familiar with high-power applications prior to this gig, I didn't understand or appreciate how contactors worked, but simple switches don't quite work for the voltage and current levels in EV packs. Even the smallest packs have a precharge circuit to avoid high current surges and arcing. Some of the conductors in these switches are quite thicc (c is for charge), as they should be.
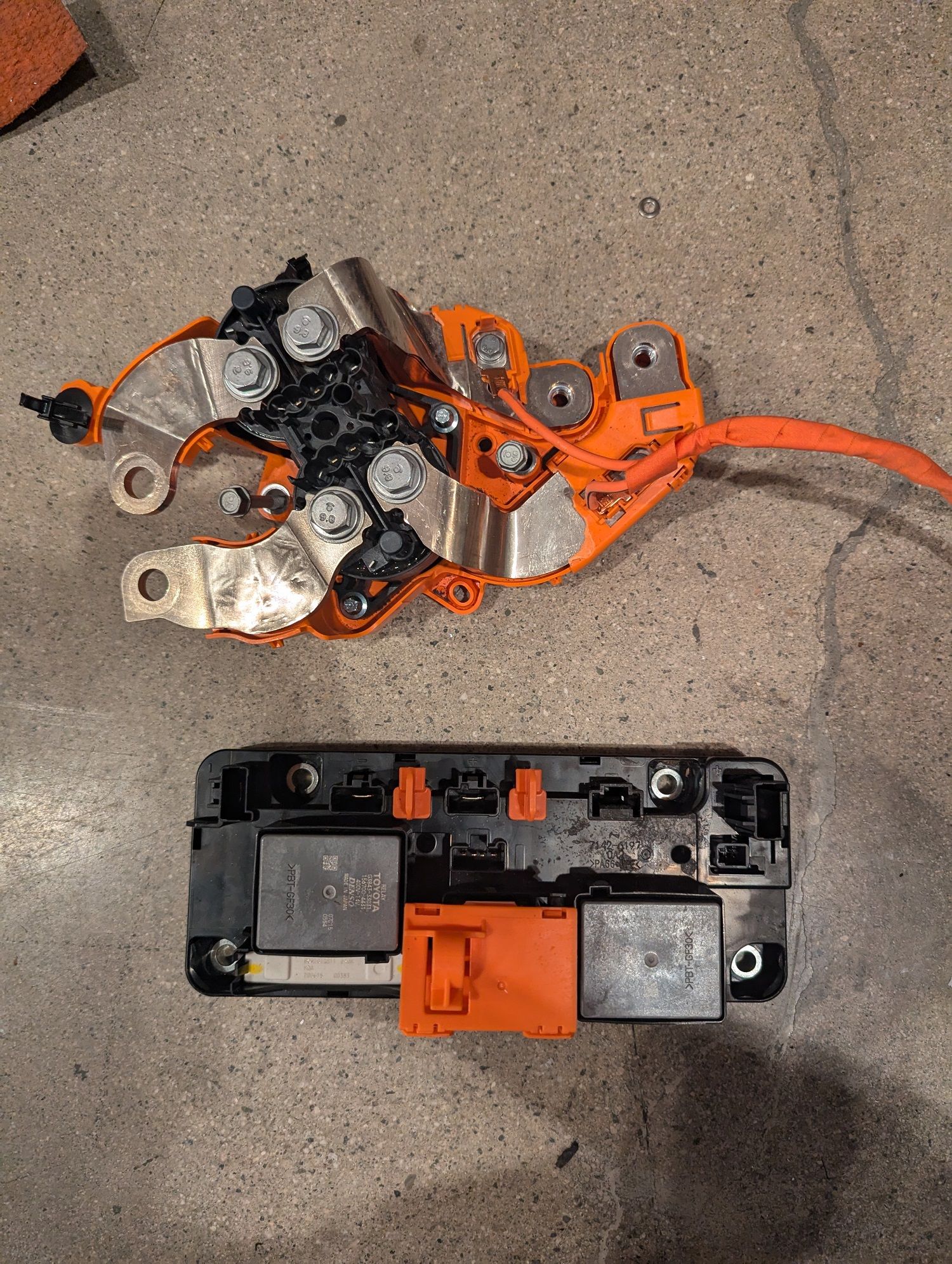
High voltage lines running between modules are fairly substantial as well. I saw some standed wire cables in older battery pack models, but most utilize chonky busbars: bent/twisted conductive bars. These are usually bolted down onto the module terminals. Being rigid, these have the added benefit of avoiding entanglement or snagging during assembly/disassembly. Most interestingly (to me), newer packs have replaced the copper in these busbars for aluminum, which I assume reduces cost and helps protect more against corrosion.
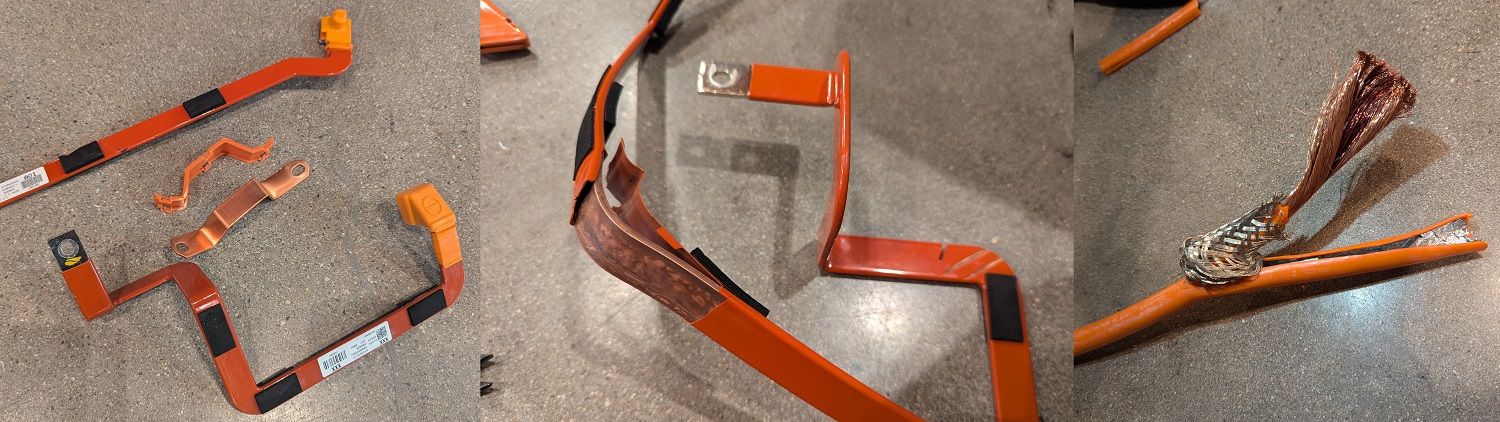
Wiring/Cabling
There's a shit ton more wires in a battery pack than I would've figured. With a whole bunch of cells, whether in series or parallel, keeping them balanced is critical to maximize longevity. Not only is there a connection to every single cell for voltage balancing, there are also intermittent sensors to prevent temperature overload and handle cooling. Smaller packs seem to route all wires to a central BMS (battery management system), which results in quite a substantial harness running across the entire pack. Larger packs are more likely to have dedicated BMS's per module, each of which then connected to a central computer.
Connectors for cabling are no joke. As you can imagine, they're designed to stay connected, not readily removed or swapped. All connectors have some sort of locking component, either compliant clips or latches. They're onerous enough that some companies make specialized maintenance pliers just to disconnect these connectors. As mentioned above, high voltage connectors are often bolted down directly to the modules.
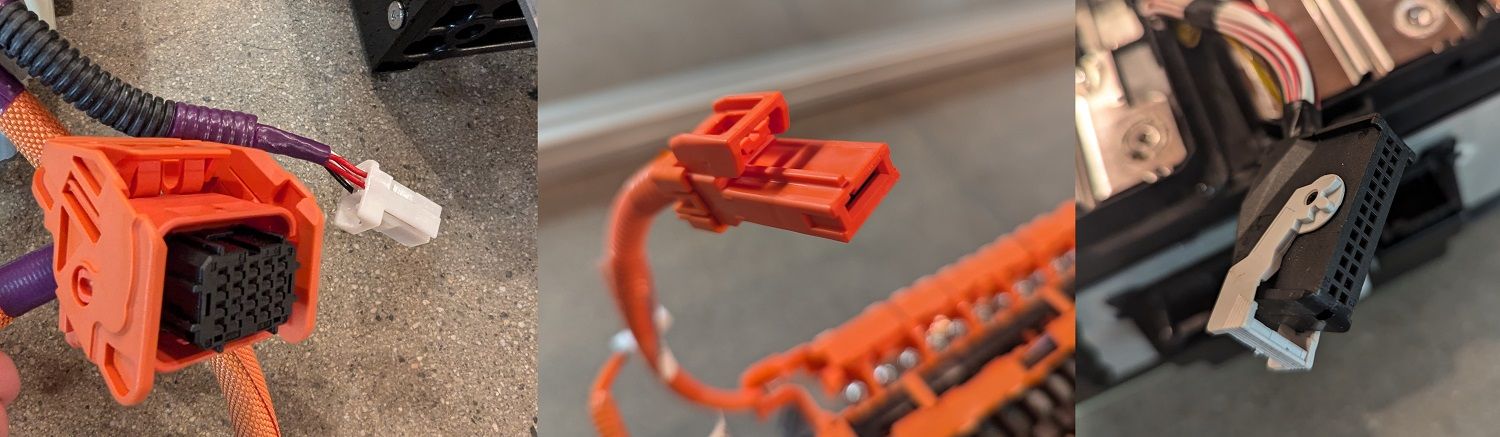
Cells within a module are usually connected via spot-welded tabs, which means destructive dismantling if the cells are to be extracted and upcycled. Older and smaller packs may utilize discrete busbar plates between adjacent cells. It does however seem like screw terminals at the cell level are on there way out as they become more integrated via increased foam usage and fastener count reduction.
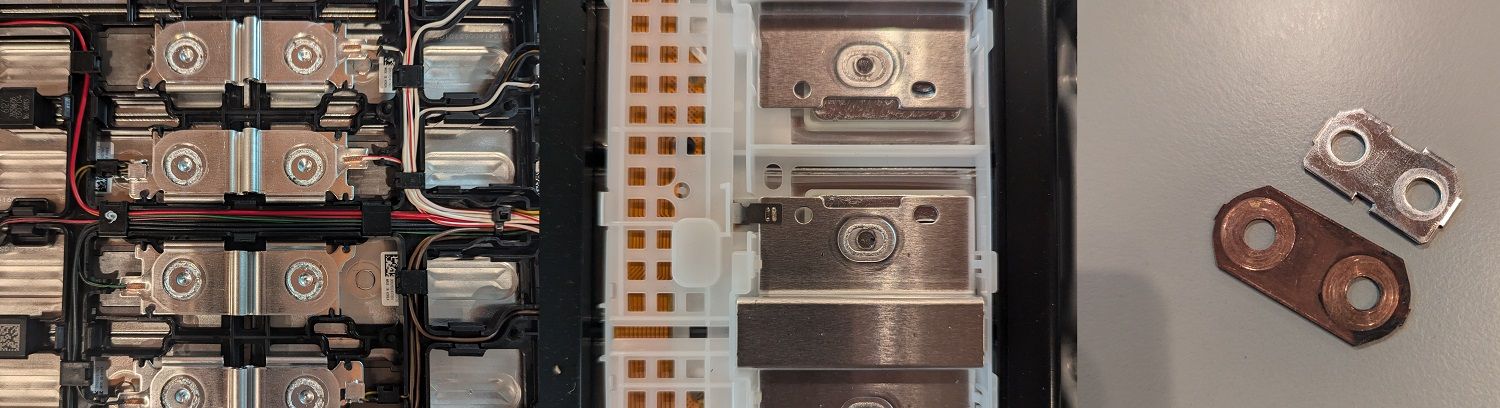
Heating/Cooling
Batteries work best within a certain temperature range, as they lose capacity/range on the lower end of the temperature range but also need to avoid excessively high temperatures when the vehicles utilizes high current. Hybrids can seemingly get away with simple forced air cooling, and there are usually some simple plastic duct covers that run along the length of the cell rows. Older full-electric models typically have channels with coolant/fluid running along the base of the pack, in contact with the modules/cells. The new Tesla models go as far as integrating cooling channels within the modules, interwoven between the cells. I should note here that draining the coolant out of the Tesla module channels was a total pain, and we got refused pickup by a shipping company the first time we didn't do it correctly. To assist in thermal transfer, there's often a paste of sorts underneath the modules.
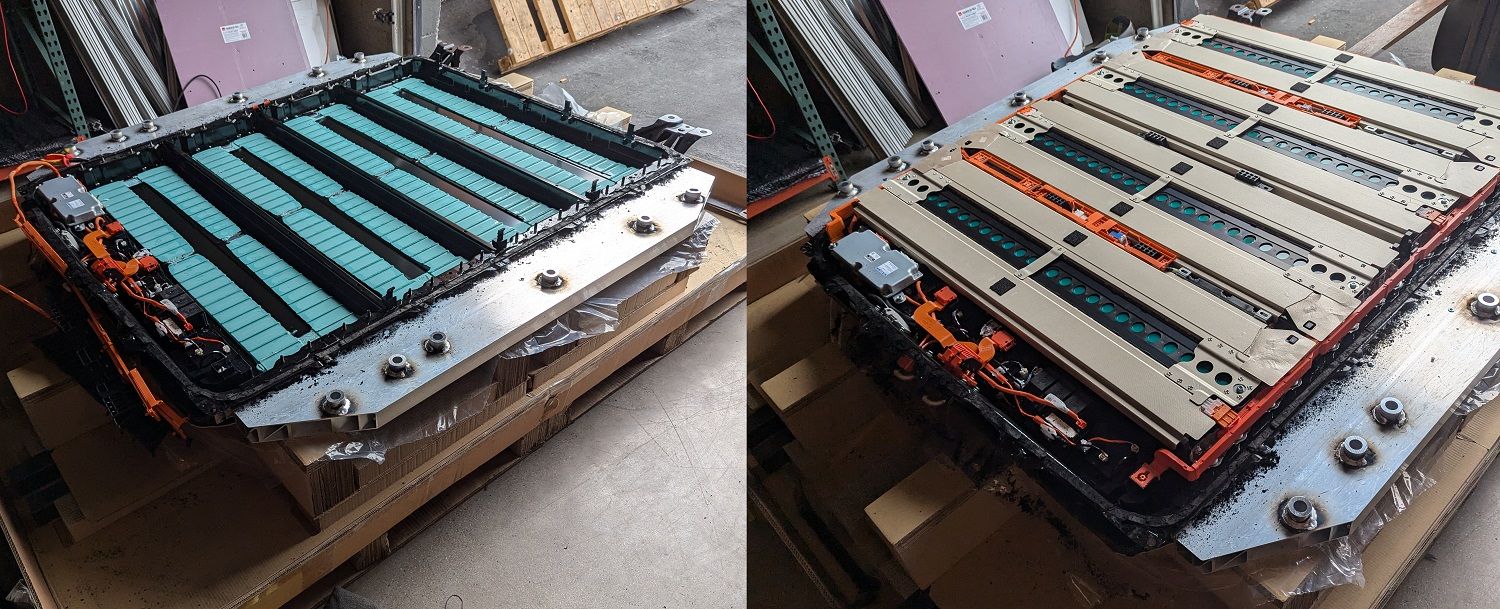
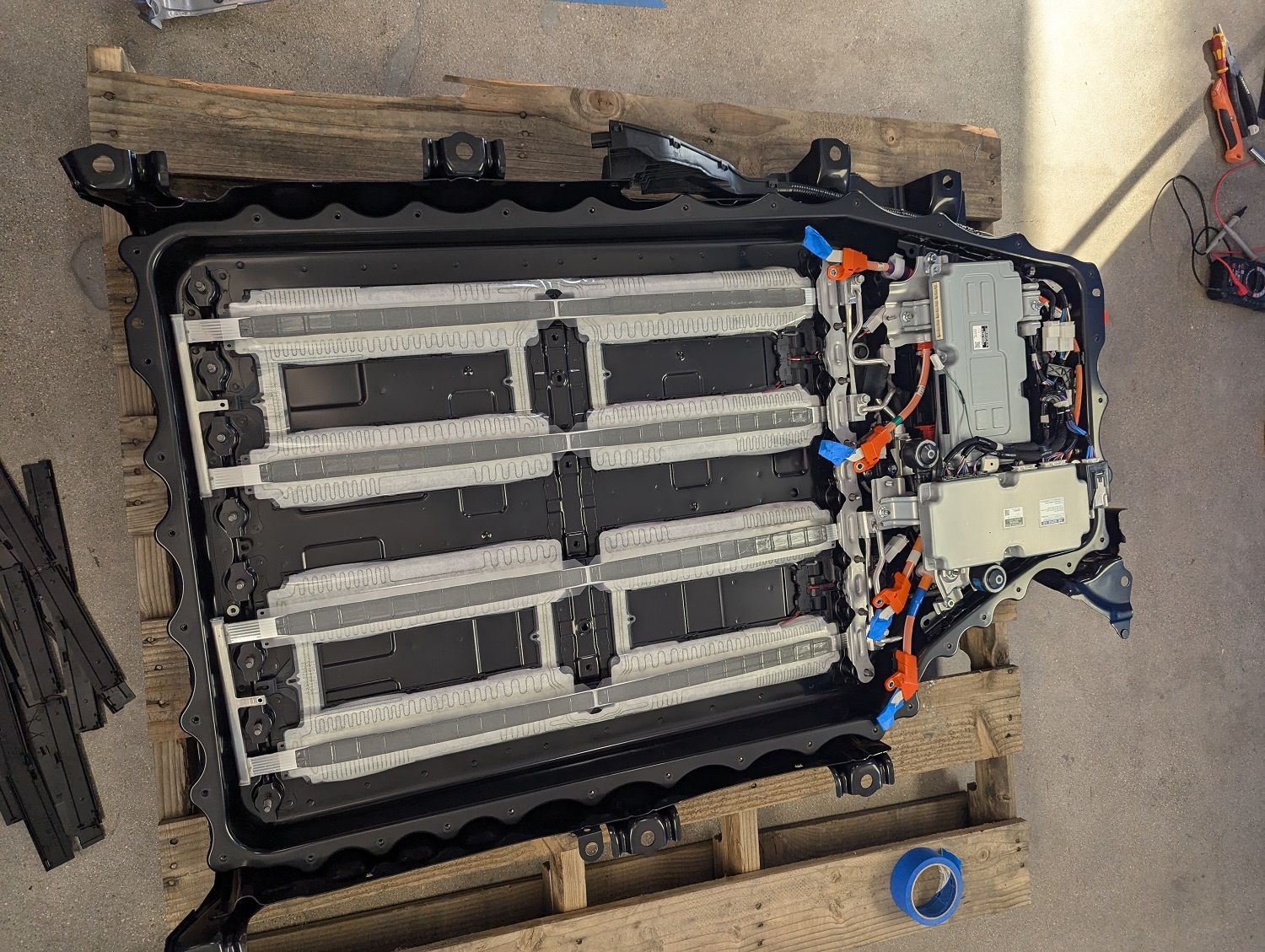
Much of the attention in the battery space has been focused on updates to chemistry and composition, but there's substantial design work on the interior layout and structure as well. Unfortunately, while the product costs (per kWh) have continued to plummet, it may come at the cost of a less repairable and accessible pack, which may put consumers in a bind later on down the road.